محققان موسسه تکنولوژی های نوآورانه الیاف و کمپانی ام ام تی تکستایلز الیافی را طراحی کرده اند که قادر است در پاسخ به رطوبت محیط فر خورده و یا به طور بر عکس باز شود.
ترجمه: آزاده موحد
به گزارش سایت نساجی امروز، در سال های اخیر استفاده از مفهوم بیومیمتیک در طراحی محصول بسیار رواج یافته است و در این رابطه محصولات نساجی بهترین و شناخته شده ترین مثال هستند.
بیومیمتیک به زبان ساده همان به کار گیری راهکارهای موجود در طبیعت برای حل مشکلات مربوط به طراحی محصولات بشرساخت است. شاید شناخته شده ترین مثال در این رابطه تکنولوژی بست های قلاب و حلقه است که در محصولات برند ولکرو محبوبیت دارد.
این بست ها از گیر کردن و چسبیدن موهای خاردار پوسته بیرونی یک دانه مشخص از گیاه به درون موهای یک حیوان در حال عبور یا پاچه های شلوار یک انسان در حال پیاده روی در میان علف های هرز، الهام گرفته شده است. لباس های شنای LZR کمپانی اسپیدو که در طول برگذاری المپیک پکن بسیار مطرح شده بود، تقلیدی از تاثیر میکرو زبری پوست کوسه در غلبه بر مقاومت آب می باشد.
اخیرا نانوتکنولوژی پوشش دهی پارچه ها با الهام از مورفولوژی سطحی برگ های نیلوفر آبی باعث افزایش قابلیت دفع آب و خود تمیز شوندگی پارچه ها شده است. البته طراحی سطوح چسبنده با تقلید از پنجه های مارمولک خانگی که به دلیل ویژگی سطحی بسیار ظریف پنجه ها قادر به بالا رفتن از سطوح عمودی می باشد هم در راه است.
اثر میوه کاج
درک تشابه الیاف و پارچه از پدیده طبیعی که تحت عنوان "اثر میوه کاج" شناخته می شود، توسط دکتر ورونیکا کاپسالی مدیر فنی کمپانی ام ام تی تکستایلز در لندن صورت گرفته و کمپانی تکنولوژی های نوآورانه الیاف واقع در جانسون سیتی ایالت تنسی، الیاف را تولید کرده است (شکل 1). در طبیعت، هنگامی که محیط رطوبت دارد، پولک های میوه کاج دانه ها را درون لایه های خود نگه می دارند اما در هوای خشک بخشی از پولک جمع شده و باعث باز شدن پولک ها و آزاد شدن دانه می شود. احتمالا و نه به صورت تصادفی به این معناست که شرایط آب و هوایی خشک برای پخش شدن دانه های کاج بهتر از شرایط مرطوب است.
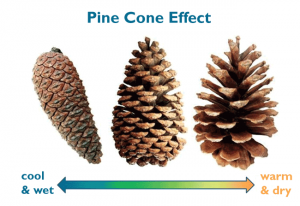
پارچه هایی که دارای ویژگی الیاف اینوتک هستند نیز طوری طراحی شده اند که بسته به رطوبت محیط به طور خودکار و قابل برگشت ساختار خود را تغییر دهند. در شرایط رطوبتی پایین نیازی به تبخیر سریع نبوده و عایق بندی حرارتی مطلوب و مورد نیاز است.
در این شرایط اندازه ی حفره های بین نخ ها در پارچه ی اینوتک مطابق معمول استاندارد پارچه های کشباف و یا تاری پودی است. چنانچه شخص شروع به عرق کردن کند و حتی در مراحل اولیه ی پیش از عرق کردن باشد، رطوبت موجود در پارچه افزایش پیدا می کند. با افزایش رطوبت نخ های اینوتک به طور خودکار جمع می شوند و فضای بیشتری بین نخ ها ایجاد می کنند و انتقال بخار ایجاد شده در پارچه را تسهیل می کنند(شکل 6). در نتیجه پوشاک به جای اینکه مانع از فرایند سرمایش تبخیری طبیعی بدن شود آن را تسهیل می کند.
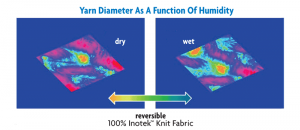
ساختار ویژه ی الیافی که نخ ها از آن تهیه می شوند باعث قابلیت انطباق پذیری در پارچه می شود. این الیاف دوجزیی و دارای مقطع عرضی غلاف/مغزی مختلف المرکز بوده که باعث می شود الیاف در پاسخ به رطوبت محیط فر خورده و یا به طور برعکس باز شوند.
الیاف غلاف/مغزی
پیش از این الیاف غلاف/مغزی مختلف المرکز در بعضی از مواردی که حرارت باعث ایجاد فرخوردگی الیاف می شود، مورد استفاده قرار گرفته اند. چنانچه حرارت اعمال شده به الیاف غلاف/مغزی متداول متحدالمرکز بیشتر از دمای انتقال شیشه ای پلیمر باشد، الیاف جمع می شوند.
نرخ جمع شدگی دو پلیمر با هم متفاوت است اما پلیمری که دارای نرخ جمع شدگی بیشتری است تنها به میزانی که توسط پلیمر با نرخ جمع شدگی پایین تر مجاز باشد، جمع می شود چون مقطع عرضی الیاف متحدالمرکز است و پلیمر با نرخ جمع شدگی بالاتر نمی تواند پلیمر دیگر را تحت فشار قرار دهد.
در الیاف غلاف/مغزی مختلف المرکز، نیروی ایجاد شده توسط پلیمر با نرخ جمع شدگی بالاتر متناسب با نیروی ایجاد شده توسط پلیمر دیگر نیست، در نتیجه با فر خوردن الیاف و ایجاد یک شکل مارپیچ، نیروها تجزیه می شوند.
این عملکرد در بعضی از موارد کاربردی مفید است اما قابلیت برگشت پذیری ندارد. الیاف تحت تاثیر حرارت وارد شده به آن ها فر خورده و به شکل مارپیچ در می آیند اما کم کردن بعدی دمای الیاف باعث باز شدن فر آن ها نمی شود.
الیاف اینوتک بر خلاف الیاف فوق که در اثر حرارت فر می خورند به رطوبت حساس ترند تا دما و فر خوردن آن ها هم برگشت پذیر است و به تناوب با افزایش رطوبت فر خورده و با کاهش آن فر الیاف هم باز می شود.
زمانی که این الیاف به صورت نخ در می آیند، فر خوردن آن ها باعث جمع شدگی نخ و کاهش قطر آن می شود که باعث ایجاد منافذ بزرگ تر بین نخ های پارچه می شود.
در حالتی که فرخوردگی در اثر حرارت ایجاد می شود، اختلاف در میزان جمع شدگی دو پلیمر باعث فر خوردن می شود. در الیاف اینوتک، فر از تفاوت در تورم یا بادکردگی که ناشی از تفاوت در میزان برداشت رطوبت یا همان رطوبت بازیافتی است، حاصل می شود.
مغزی این الیاف پلی پروپیلن بوده که تقریبا فاقد رطوبت بازیافتی می باشد حتی در شرایطی که رطوبت بالاست. پوسته الیاف نیز نایلون 6 بوده که رطوبت بازیافتی آن وابسته به رطوبت محیط است؛ در رطوبت نسبی 98%، حداکثر رطوبت بازیافتی 5/4% وزنی می باشد. با جذب آب توسط نایلون پلیمر باز می شود. با یک بازشدگی نسبتا کوچک فشارهای مورد نیاز برای فر خوردگی الیاف حاصل می شود.
فرایند تولید الیاف
هرچه فر ایجاد شده در الیاف بیشتر باشد، تاثیر آن در پارچه حاصل بیشتر قابل مشاهده است. بنابراین در فرایند تولید الیاف توجه خاصی به چگونگی بهینه سازی مقدار فر ایجاد شده می شود.
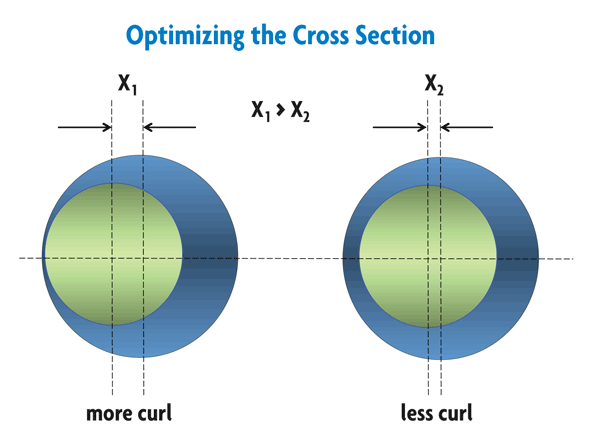
درجه فرخوردگی تا حد زیادی تحت تاثیر فاصله بین مرکز جرمی دو پلیمر است (شکل 2). بنابراین بیشترین میزان فرخوردگی در اثر مقطع عرضی پهلو به پهلو حاصل می شود نه مقطع عرضی غلاف/مغزی مختلف المرکز. البته داشتن مقطع عرضی پهلو به پهلو در الیاف اینوتک مفید نیست چون در این حالت دو پلیمر برای اینکه بتوانند وحدت خود را به عنوان یک لیف حفظ کنند که این امر لازمه فر خوردن الیاف است، تنها در خط واصل خود می توانند به هم بچسبند.
متاسفانه چسبندگی بین نایلون و پلی پروپیلن چندان خوب نیست و فشارهای ناشی از تورم نایلون برای جدا کردن دو پلیمر و تبدیل آن ها به الیاف جداگانه کافی است، در نتیجه نیروهای لازم برای ایجاد فر از بین می روند. علاوه بر این چنانچه دو جزء پیش از فرایند کاردینگ و ریسندگی نخ از هم جدا شوند، امکان تبدیل درست لیف به نخ وجود نخواهد داشت.
بنابراین تا زمانی که در الیاف غلاف/مغزی فاصله بین مراکز جرمی دو جزء به اندازه کافی برزگ باشد، امکان قرار گرفتن پلی پروپیلن درون نایلون وجود خواهد داشت که این امر مانع از لایه لایه شدگی می شود. گام بعدی در طراحی الیاف غلاف/مغزی با توجه به محدودیت های آن، چگونگی به حداکثر رساندن میزان مختلف المرکز بودن است.
هل دادن بیش از حد مغزی به یک طرف مقطع عرضی ریسک شکاف برداشتن دیوار بیرونی پوسته را در نازک ترین نقطه آن به همراه خواهد داشت و امکان لایه لایه شدن پوسته را از قسمت مغزی افزایش خواهد داد. محققان موسسه تکنولوژی های نوآورانه الیاف باید به دنبال راهی می بودند که تا حد امکان مغزی را از مرکز دور می کردند بدون این که باعث نازک شدن بخشی از پوسته شوند تا حدی که مغزی بتواند از پوسته خارج شود.
در بررسی مقطع عرضی الیاف پس از فرایند اکستروژن، پوسته ی بعضی از مقاطع عرضی به طور نامحسوسی نازک بوده و یا حتی دارای شکاف بسیار اندکی است که البته احتمال لایه لایه شدن آن بسیار کم می باشد اما در فرایندهای بعدی پس از اکستروژن شامل تجعد مکانیکی، کاردینگ، ریسندگی نخ، کشبافی یا بافندگی تاری پودی و حتی خشکشویی و فرخوردن مجدد و باز شدن آن در پوشاک، یک سری نیروهای فیزیکی وجود دارد که در صورت نازک بودن ظریف ترین بخش "دیوار نگهدارنده" باعث تشدید تمایل به لایه لایه شدن می شود.
نخستین انتخابی که موسسه در بررسی بهینه سازی مقطع عرضی مد نظر قرار داد آسان ترین انتخاب بود؛ تولید الیاف با مغزی های کوچک تر. تا زمانی که مرکز مغزی سر جای خود باقی بماند و جدا شدن آن از مرکز پوسته انجام شود، کاهش قطر به معنای افزایش ضخامت دیوار نگهدارنده است.
البته آزمایشات نشان داد که عملکرد فرخوردگی این الیاف کمتر است. محققان همچنان به دنبال راهی برای حفظ جایگاه دیوار نگهدارنده و در عین حال به حداکثر رساندن جداسازی مراکز جرمی پلیمرها بدون کاهش یافتن جرم کلی مغزی بودند. این ساختار نیازمند اصلاحات چالشی جدی بر روی شکل مغزی پلی پروپیلن بود.
خوشبختانه موسسه تکنولوژی های نوآورانه الیاف دارای توانایی استثنایی در ایجاد تغییرات بسیار دقیق و نامحسوس در مقطع عرضی الیاف دو جزیی است و در نتیجه موفق شد تا هم خاصیت فر خودن الیاف و هم مقاومت آن ها در برابر لایه لایه شدن را بهبود بخشد.
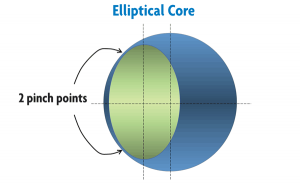
موسسه با اعمال کنترل دقیق بر روی مقطع عرضی، الیاف دارای مغزی بیضوی را مورد بررسی قرار داد (شکل 3). تبدیل فرم دایره ای مقطع عرضی مغزی به فرم بیضی راهیست برای دورتر کردن مغزی از مرکز الیاف بدون آن که شکافی در پوسته ایجاد شود. محققان با این تحقیق متوجه شدند که اگرچه ایجاد مغزی بیضوی نسبت به حالت دایره ای آن یک پیشرفت محسوب می شود اما با این حال معایبی هم دارد برای مثال لبه ی بیرونی بیضی همچنان با لبه ی بیرونی دایره ای شکل الیاف مطابقت ندارد که این امر منجر به ایجاد "نقاط فشرده شده" می شود که در آن جا پوسته به طرز خطرناکی نازک است.
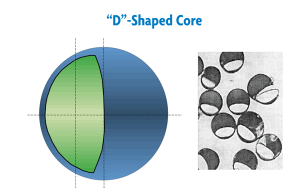
محققان با ایجاد مغزی D شکل در جستجوی راهی برای غلبه به این نقاط بوده اند (شکل 4). این فرم از مغزی باعث حفظ ثبات ضخامت پوسته در طول نازک ترین بخش آن می شود. مغزی دارای یک سر مخالف است که صاف بوده و میزان جداسازی مراکز جرمی پلیمرها را به حداکثر می رساند.
البته گوشه های نسبتا تیز که در آن جا شکل دایره ای به خطی تبدیل می شود باعث ایجاد نقاط پارگی می شوند که نیروهای سایشی می توانند در آن جا جمع شده و منجر به ایجاد شکاف پوسته در آن نقاط شوند.
در نهایت محققان با در نظر گرفتن جدا سازی مراکز جرمی تصمیم گرفتند که با گرد کردن تیزی گوشه ها و لبه ی نسبتا صاف مغزی D شکل، یک حالت متعادل ایجاد کنند. نتیجه، ایجاد یک مغزی با لبه ی بیرونی دایره ای شکل بود که نقاط منحنی آن تا حدی از شکل بیضوی لبه داخلی فاصله داشت. این شکل را می توان D بیضوی نامگذاری کرد (شکل5). مقطع عرضی فوق بیشترین میزان فرخوردگی قابل بازگشت در اثر رطوبت را ایجاد می کند و در فرایندهای بعدی نیز مشکلات مربوط به لایه لایه شدن را هم ندارد.
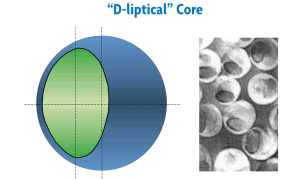
پارچه های تهیه شده از این الیاف دارای قابلیت تنفس پذیری انطباقی بوده و در مناطق حاوی منافذ باز این پارچه ها هم تغییرات چشمگیری ایجاد شده است که در نتیجه ی آن قابلیت نفوذ هوا در پارچه در اثر رطوبت محیط نیز تغییر کرده است.
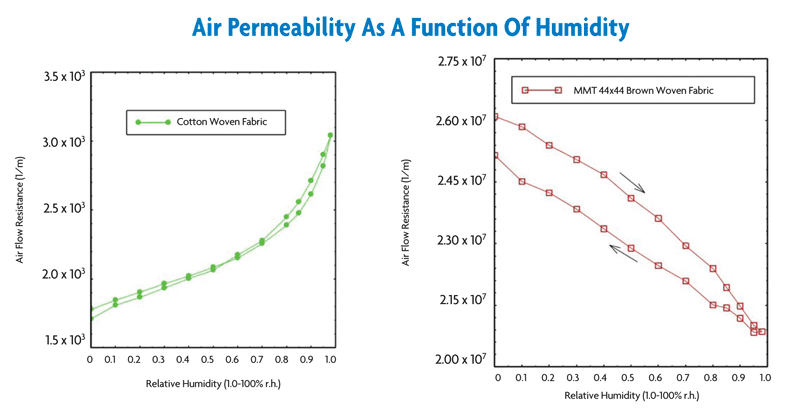